· JS · English · 2 min read
EL inspection in Spain
Solarzentrum Stuttgart inspects modules after delivery at four 50 MWp PV sides in Spain.
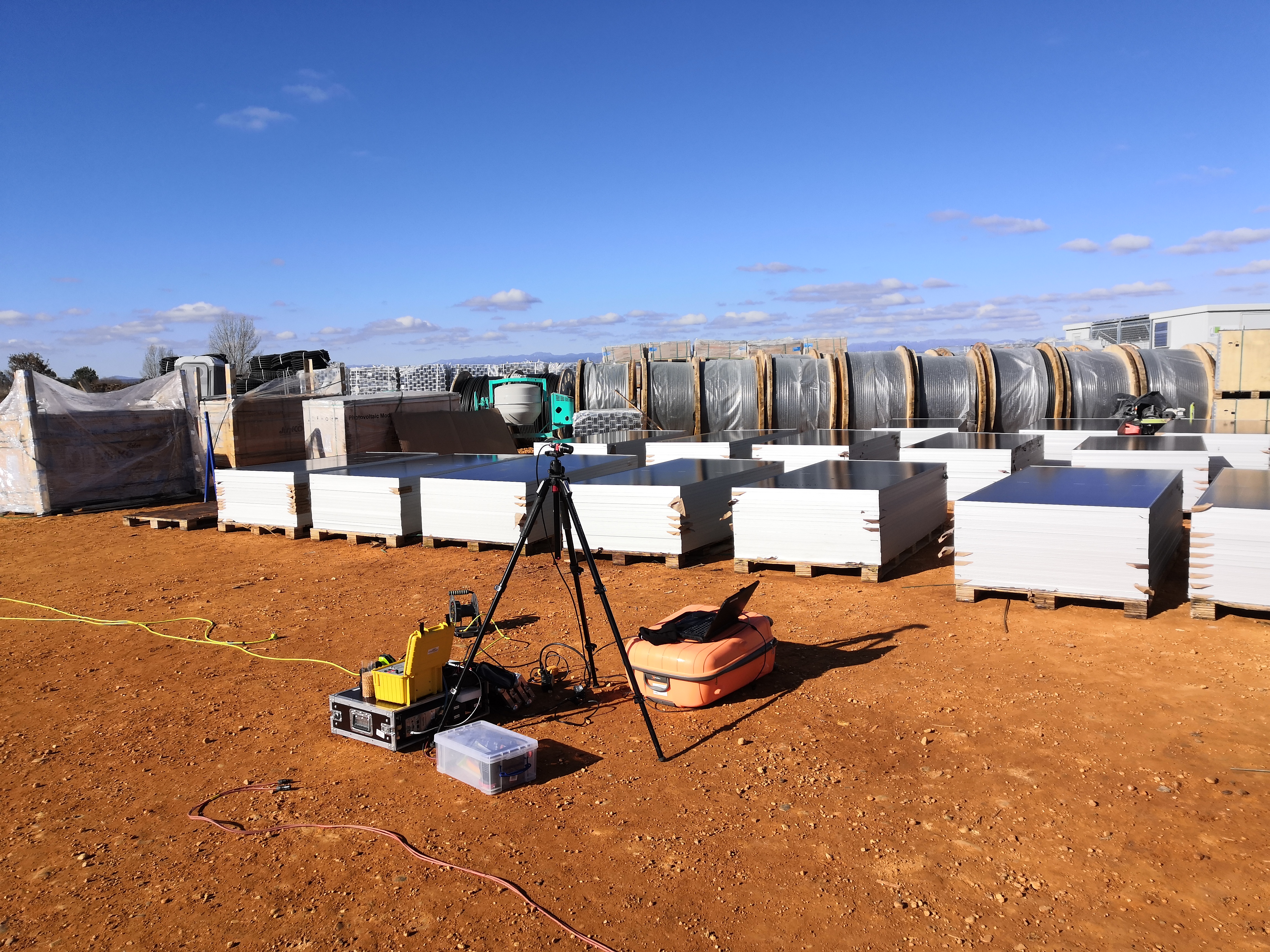
Electroluminescence inspection in Spain
In January, the ‘Solarzentrum Stuttgart’ carried out an electroluminescence (EL) inspection of PV modules after their delivery in Spain. The inspection was performed over four days at four different PV parks under construction, each with a capacity of around 50 MWp.
The specialist from Solarzentrum Stuttgart, J. Schramm, flew to Spain with the necessary measuring equipment to carry out the inspection. The approved DaySy measurement equipment was used, which enabled a detailed inspection of the modules in daylight.
A key advantage of daylight electroluminescence is its flexible use without containers. It also enables a high throughput of up to 200 modules per working day, even taking into account the unpacking and restacking of the pallets. With prepared module stacks, a throughput of 500 modules per working day can be achieved.
On delivery, visible damage was found on the pallet packaging, indicating possible transport damage. Visible glass cracks caused by contact with a forklift truck, for example, can be quickly identified. However, it is essential to perform an EL inspection of the neighbouring modules without visible damage. The EL inspection detects cell cracks, which can lead to a loss of performance. As the modules are palletised vertically on the long side, five modules on each side of the pallet were inspected with EL.
At the beginning of the day, the DaySy measuring system was set up near the modules to be tested and made ready for use while the pallets to be measured were unpacked. The inspection was carried out systematically in several steps. First, two workers each carried a PV module to the measuring point to prepare it for the inspection. The module was supplied with power by connecting it to the DaySy unit. Before each inspection, the serial number of the module was scanned to ensure exact allocation and to document the results in a traceable manner. A high-resolution EL image of the module was then taken with our special camera. While two workers brought the next module to the measuring point, two others stacked the already tested module on a pallet.
The collaboration with the client went smoothly. The logistical challenges of the process were mastered together. The results of the EL inspection provide valuable information about the quality of the modules supplied and help to ensure the performance of the PV plant.
Special thanks go to everyone involved for their outstanding cooperation and commitment on site!